Maximizing Reliability Efficacy through Effective RCFA Execution
Posted By:
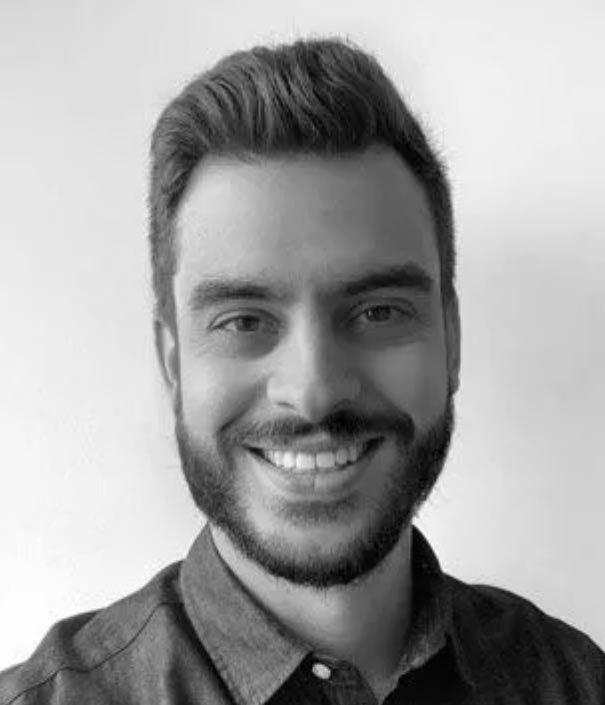
In the mining industry, operational efficiency is a cornerstone, and achieving it requires a unique approach, depending on the site-specific requirements and limitations. Root Cause Failure Analysis stands out as a powerful tool within the reliability realm, enabling sites to identify and address the root causes of their equipment failures systematically.
Root Cause Failure Analysis, or RCFA, goes beyond addressing surface-level symptoms, focusing on the core issues that trigger failures. This methodology empowers reliability and maintenance departments to implement targeted solutions, ultimately boosting operational reliability and availability.
Effective RCFA Execution
1. Robust Data Collection
Fleet operation and maintenance data are ideally being compiled in the background. That usually includes, but is not limited to, FMS system, equipment monitoring, and CMMS data. Operating equipment generate vast amounts of data, and utilizing this information is crucial. From its performance metrics to maintenance records and operating procedures, thorough data collection sets the stage for a detailed analysis.
2. Clear Objectives
Define precise objectives before starting an RCFA. Clearly identifying which issues or failures to address during the activity streamlines the analysis process and ensures focus on the most critical aspects of reliability improvement. It is highly recommended to identify triggers that will dictate the necessity of a RCFA, such as repetitive failures, safety and environmental incidents, or near misses.
3. Cross-Functional Team
Assemble a diverse, cross-functional team for an effective RCFA. Experts from maintenance, operations, engineering, and safety bring unique insights, with each perspective enriching the analysis process.
4. Analytical Tools and Techniques
Depending on the resource and data availability, there are various tools that can be utilized to get to the bottom of the target issue. Tools can range in complexity, from a more advanced method such as Failure Mode and Effects Analysis (FMEA) to simpler methods such as the 5Ys and fishbone methods. The intent of an RCFA is always to explore potential failure scenarios comprehensively. These tools facilitate narrowing down to the most likely root cause or the combination of multiple reasons.
5. Thorough Documentation
Document the RCFA process, findings, and recommended solutions thoroughly. This documentation serves as a roadmap for future reference and supports knowledge transfer and continuous improvement.
6. Implement Sustainable Solutions
An RCFA's goal is to implement sustainable solutions to prevent recurrence of failure. Solutions, whether changes in maintenance procedures or equipment adjustments, should be practical and tailored to address identified root causes.
7. Continuous Monitoring and Improvement
Implement a robust monitoring system for continuous assessment. This ensures that solutions remain effective and allows for adjustments as operational conditions evolve.
Mastering effective Root Cause Failure Analysis is pivotal in the mining industry's pursuit of operational excellence. By adopting a systematic, data-driven approach, mine sites can uncover root causes, leading to enhanced reliability, reduced downtime, and sustained operational efficiency. Outliers is prepared to help with developing and implementing a RCFA process that matches your specific site requirements.
Connect with an Outlier
Subscribe to our monthly newsletter!
All Rights Reserved