Prioritize Work with an Equipment Criticality Assessment
Posted By:
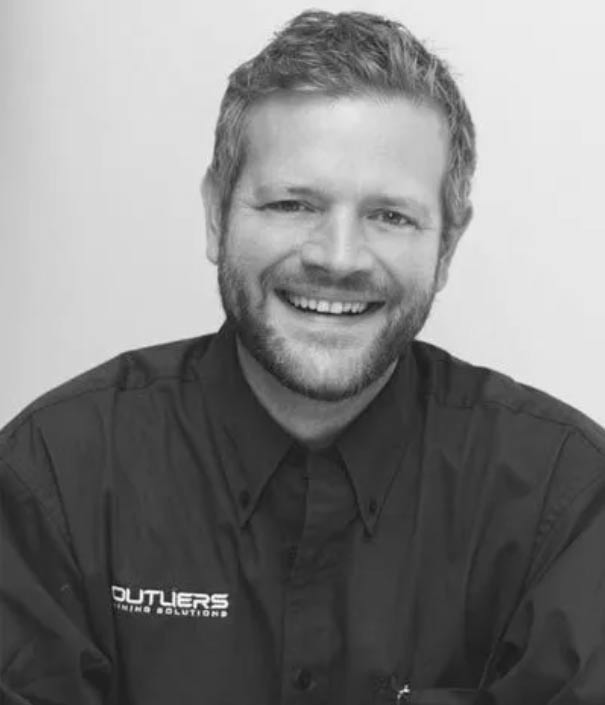
Work prioritization continually changes based on the evolving needs of the business. A component of prioritizing work is Equipment Criticality. A Criticality analysis is defined as the process of assigning assets a criticality rating based on potential risk and consequence of failure.
Why is criticality analysis important?
Criticality plays a role in nearly all types of maintenance. It narrows down to risk and what makes each piece of equipment critical, letting you understand the asset’s potential risks that could impact your operation. Utilizing a risk-based magnifying glass of sorts to ensure reliability rather than considering opinion based risk evaluation. As a foundational component, criticality assessment is the basis of sound maintenance practices.
However, it also underpins:
- OPEX management
- Impact on safety and environment
- Ability to isolate single-point failures
- Prioritization of operations and maintenance history
- Understand mean time between failures
As the criticality models deal with multiple areas of the organization, a criticality analysis should be a company-wide effort. Including departments that deal with operations, engineering, maintenance, procurement, and health and safety ensures that the analysis considers operational functions as a whole.
Criticality analysis is also important because it can be used strategically during various scenarios within an organization. For example:
- Criticality score can be employed as an input to help determine the final priority ranking for maintenance tasks, which in turn can be used together with work order priority.
- Can help to identify high-level risk mitigation strategies for specific equipment. This can involve applying condition monitoring techniques to high-criticality assets.
- Can help optimize the number of spare parts for each piece of equipment.
- It can provide valuable input for budgeting discussions, so high-criticality equipment is prioritized for upgrades or replacement.
- Can help reliability practitioners focus their efforts and energy on the most critical assets.
Performing Criticality Analysis
In order to perform the analysis, three steps are required:
Agree on the risk matrix. This mainly refers to existing corporate risk matrices and how most of these matrices may need to be adjusted to include an equipment criticality assessment. Two key areas where modification might be needed are agreeing on risk levels from a corporate and equipment level, and combining the overlapping risk categories. On a corporate level, a failure that leads to a loss of $1 million in revenue might be considered minor or moderate, but on an equipment or facility operational level, it might be seen as major, if not catastrophic, to reliability and availability targets.
When laying out criticality rankings visually, there are many theories on the best way to do this. One of the most common approaches is to use a grid, which plots the probability of failure against the severity of failure, resulting in a risk priority number.
A more comprehensive approach is to evaluate all major risk criteria (health, safety, environment, reliability, etc.). This type of complex analysis will require a multi-disciplined team.
Let Outliers help you build a training program to facilitate such work. We train for certainty and educate for uncertainty.
Connect with an Outlier
Subscribe to our monthly newsletter!
All Rights Reserved